words Al Woods
Servo motors have been around for over a hundred years, helping to transform the industrial world. The original servo motors were large and weak when compared to the servo motors we use now.
Today, servo motors take the form of small, powerful, and energy-efficient devices used in robotics, manufacturing, and the pharmaceutical and food industries.
Servo motors have proven to be an essential piece of gear that has helped many industries scale up with phenomenal speed. New levels of efficiency and productivity have been reached utilizing their power.
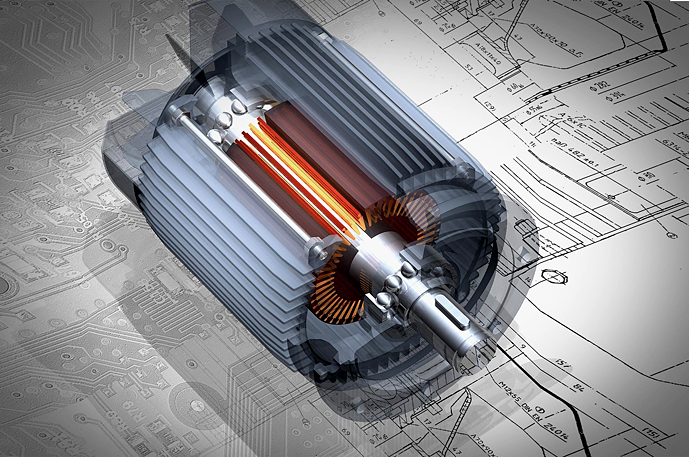
What Is a Servo Motor?
Servo motors are utilized for pushing or rotating objects with incredible precision. If you have an application that requires an object to be pushed and rotated at precise angles or distance, then a servo motor is adept.
The motor is quite simple and runs through a servo system. A DC powered motor is called a DC servo motor, and an AC powered motor is called an AC servo motor. Modern servo motors are capable of producing very high torque yet are small and light in their design. This performance capability has made servo motors incredibly useful for many technologies and across many industries.
Servo motors are most commonly used for:
- In-line manufacturing robotics
- Pharmaceutical and food production
- Flying drones (remote-controlled helicopters/planes)
- Robots
- Airplanes
Servo motors are measured in kg/cm (kilogram per centimeter). The kg/cm indicates how much weight the servo motor can shift at a specific distance.
For example, a 7.5 kg/cm servo motor can lift 7.5kg when the load is suspended 1cm away from the shaft. The motor shaft is positioned at a precise angle using the control signal. Today, manufacturers have started to produce servo motors designed for incredibly useful applications such as robot arms, drones, in-line manufacturing robotic automation, or any object required to move at a precise angle.
How Do Servo Motors Work?
The circuitry is built inside the servo motor unit with a positionable shaft. This shaft is typically fitted with a gear. An electric signal controls the motor, which then determines the movement of the shaft.
The electrical pulse width modulation (PWM) controls the servo motor through a control wire. This pulse is made up of a minimum pulse, maximum pulse, and repetition rate. Servo motors typically move at a 90° either way for a 180° movement. The neutral position is where the servo has equal rotation capability in either direction.
The position of the shaft is determined by the electrical pulse when sent to the servo motor. Depending on the duration of the pulse, sent via the control wire, the rotor can turn to the desired position with high precision and speed.
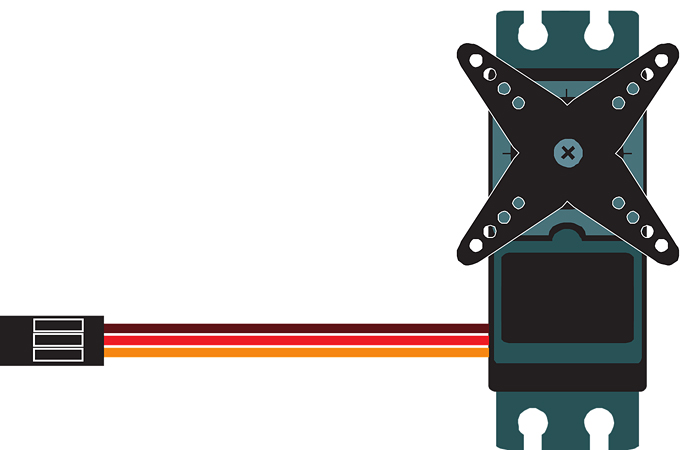
The Difference Between a Motor and a Servo Motor
There are some key differences between a regular DC motor and a servo motor. These can be broken down by the following factors.
Wire System
DC motors are made up of a two-wire system, known as a power and ground system. A servo motor has a three-wire system, known as power, ground, and control.
Assembly
A DC motor is an individual machine that requires no assembly. This differs from a servo motor, which has four parts: motor, gearing set, control circuit, and position sensor.
Rotation
A DC motor rotates on a continuous basis. A servo motor is limited to 180° and does not rotate freely or continuously like a DC motor.
DC motors are in cars, wheels, various tools, wind turbines, and appliances, where continuous rotation is useful. Servo motors are designed to help with precision movements such as that of a robotic arm or drone.
Therefore, a servo motor is much like a DC motor, but it doesn’t run continuously. Instead, it runs precisely as and when it needs to, which can significantly improve energy efficiency and skill of work completed. For these reasons, servo motors are extremely useful for the automating industry, where large quantities of objects require ultra-fast and precision work.
Servo Motor Accuracy
The typical accuracy of a servo motor is around +/-0.05 deg. This achieved with an encoder. The motor rotates, and an electrical signal is delivered to the servo driver, which informs it on its current speed and position. A servo motor is only ever as accurate as it’s encoder’s accuracy.
When comparing a servo motor to AC or DC motors, servo’s have a clear advantage in terms of speed, high peak torque, and acceleration. A servo motor is capable of operating at speeds of up to 5,000 rpm or more. The closed-loop positioning capability far exceeds the typical positioning capabilities of other speed motors and drives.